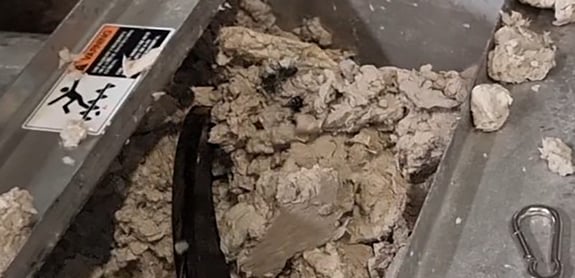
Dewatering Press
The FOURNIER ROTARY PRESS™ offers a highly efficient solid-liquid dewatering separation for a range of industries that handles biomass, sludge, pulp, or other suspension materials.
An efficient and economical dewatering solution.
The Fournier Rotary Press™ is a solid-liquid separation technology that significant advantages over traditional dewatering solutions. With distinct models suitable for high fiber-containing sludges (CVP) and biological sludges (CVH), it offers a highly effective dewatering process that uses less polymers, power and water compared to other technologies.
The installation of the rotary press requires a smaller footprint and boasts a modular and expandable design, providing cost-effective expansion opportunities as capacity demands grow. Additionally, its slow rotational speed results in lower noise and reduced vibrations, enhancing the work environment and simplifying installation-site requirements.
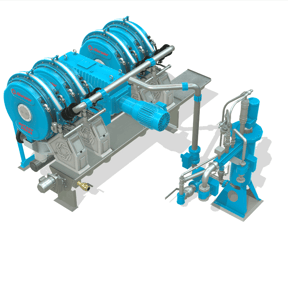
PERMANENTLY REDUCED OPEX
Capable of handling 0.5% to 10% inlet consistencies, it can replace pre-thickening and main dewatering equipment.
Recognized for best-in-class operational flexibility and low OPEX, its enclosed design prevents odor emissions and maintains a clean machine environment. High automation possibilities and reliability minimize operator attendance, freeing up time for other worktasks.
Lab and pilot tests ensure sound performance data at an industrial scale.
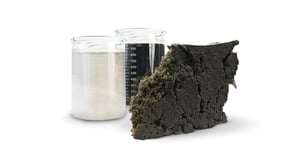
TECHNICAL INFO
The Fournier Rotary Press™ is a enclosed system completed by sludge and polymer feed systems.
The operation principle of the press is quite straightforward with few moving parts that rotates at a slow speed (around 1 r.p.m);
Flocculated sludge is introduced into a channel under low pressure and set into motion between two parallel, revolving stainless steel chrome-plated filter elements. The process allows free water to filter out while the sludge thickens and dehydrates further as it progresses through the channel. The accumulation of flocculated sludge against a restrictor arm gradually builds pressure. This pressure, in tandem with the frictional force from the slow-moving filter elements and the controlled restriction of the outlet, creates sufficient back pressure to intensify dewatering, culminating in the extrusion of an exceptionally dry cake.
KEY METRICS:
▶️ Slow rotation speed: 0.5 to 2 rpm.
▶️ Cake total solids percentage varies: 15% to >58% based on sludge type.
▶️ Filtrate total suspended solids capture rates: 95% to 99.5%, dependent on sludge type and polymer usage.
▶️ Minimal internal abrasion, even with abrasive sludges.
▶️ Energy consumption ranges: 2 to 7 kW/hr per dry ton of sludge.
▶️ Flow rates per hr/dewatering module: 2 to 12 m3/hr, dependent on sludge type and dewaterability.
▶️ Optimized polymer consumption.
▶️ Recognized for the lowest operational expenses across the life cycle compared to competing technologies.
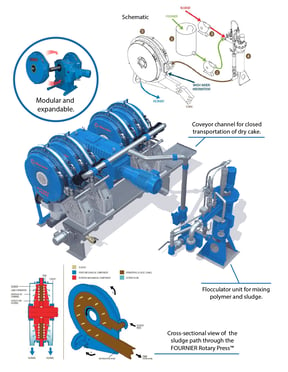
Products
The FOURNIER ROTARY PRESS™ offers a highly efficient solid-liquid dewatering separation for a range of industries that handles biomass, sludge, pulp, or other suspension materials.
Wide selection of quality pumps and flow solutions for all stages of the process-line.